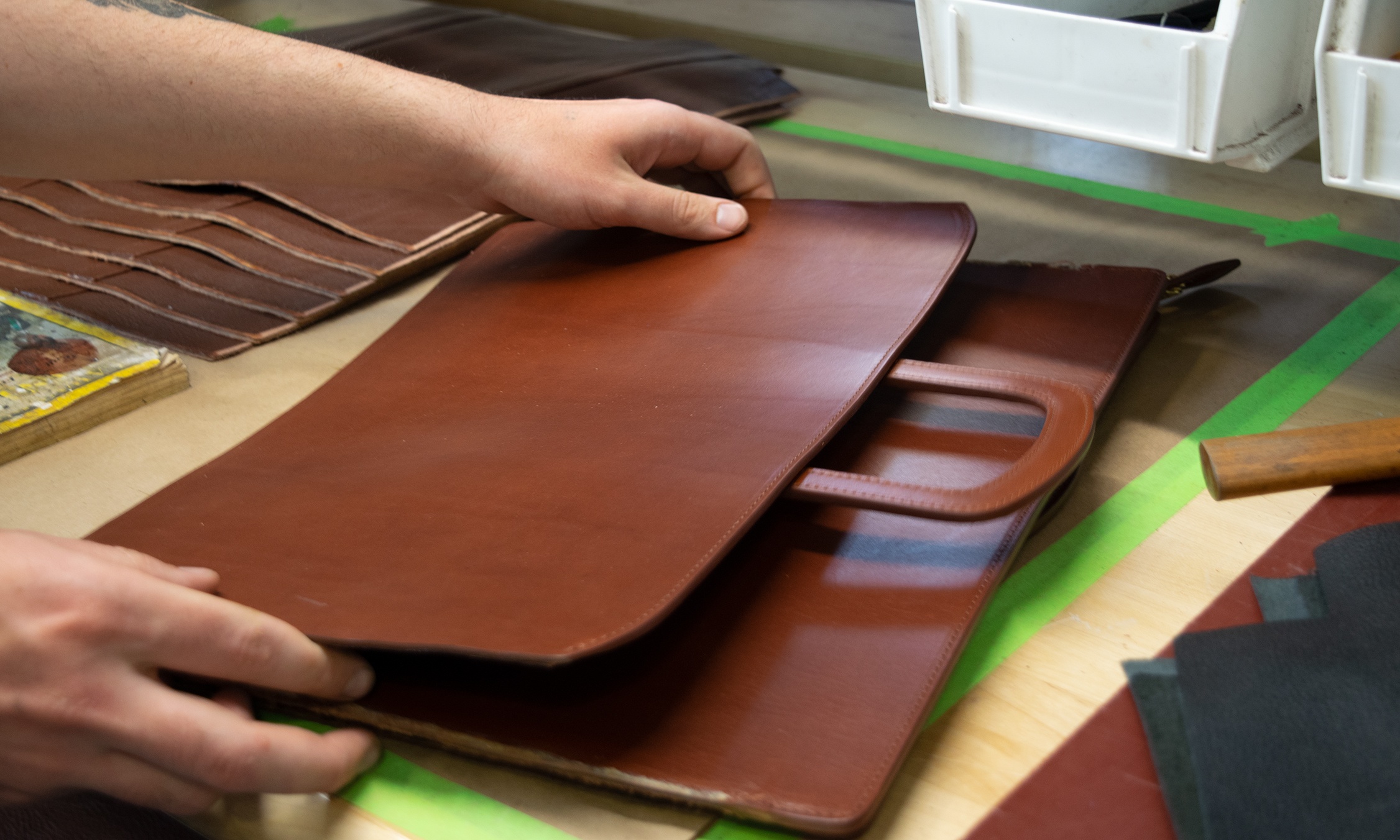
Today in the studio, our run of Wells briefcases are making a stop at the assembly station. With all its smooth, aerodynamic lines, the Wells is what happens when mid-century modern design meets a business bag, and so it needs to have perfect weight distribution to function and appear as it should. A big part of this comes into play at assembly, where all its pieces are matched and fit together before carrying on to be stitched.
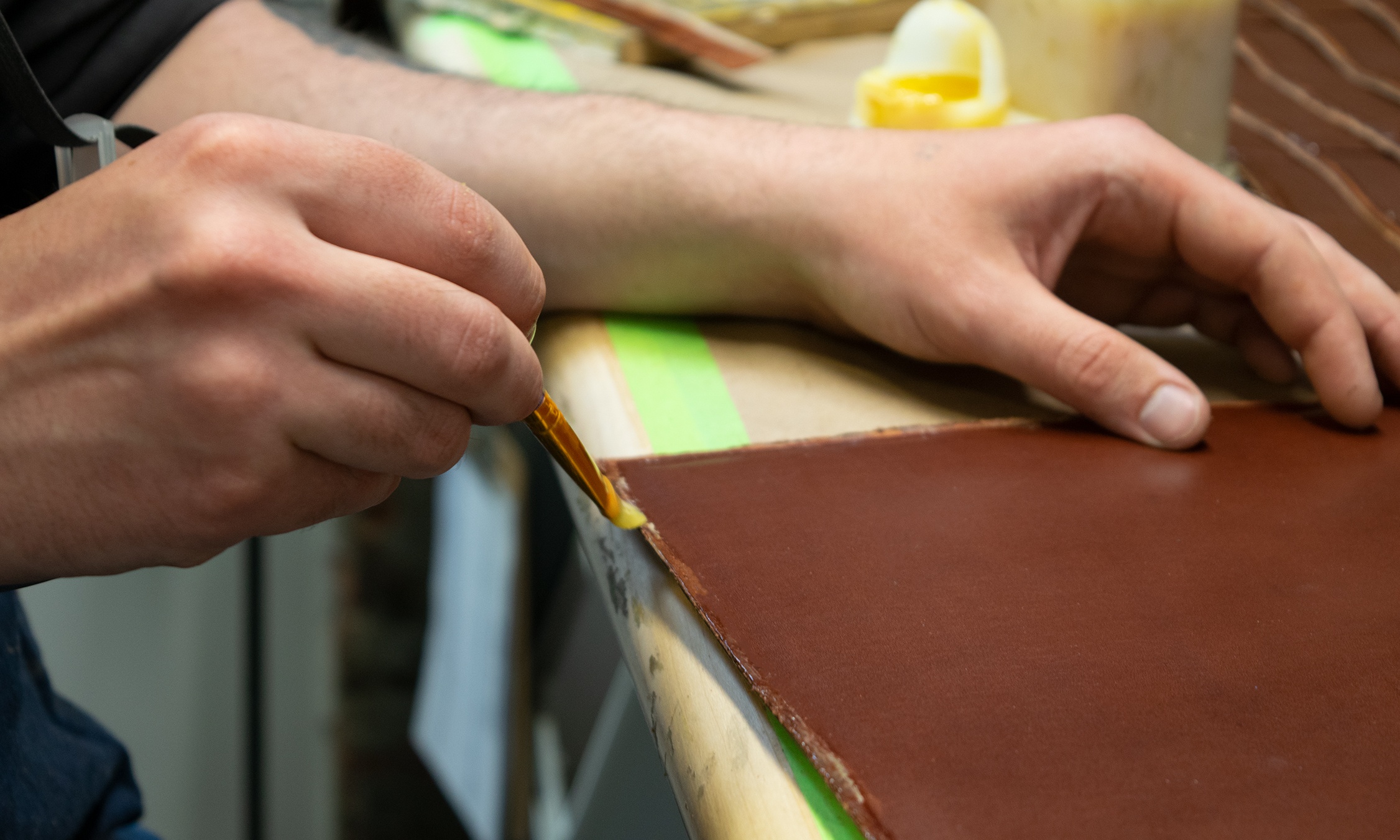
Some of this work has already been taken care of during splitting, where our tolerance for weight discrepancies amongst split pieces is less than one percent! But it’s here that artisans like Jon and Jessie precisely measure and line up the Wells’ sides to verify that the weights are even for each given bag and that the already-attached handles will fluidly drop down into their slots as needed.
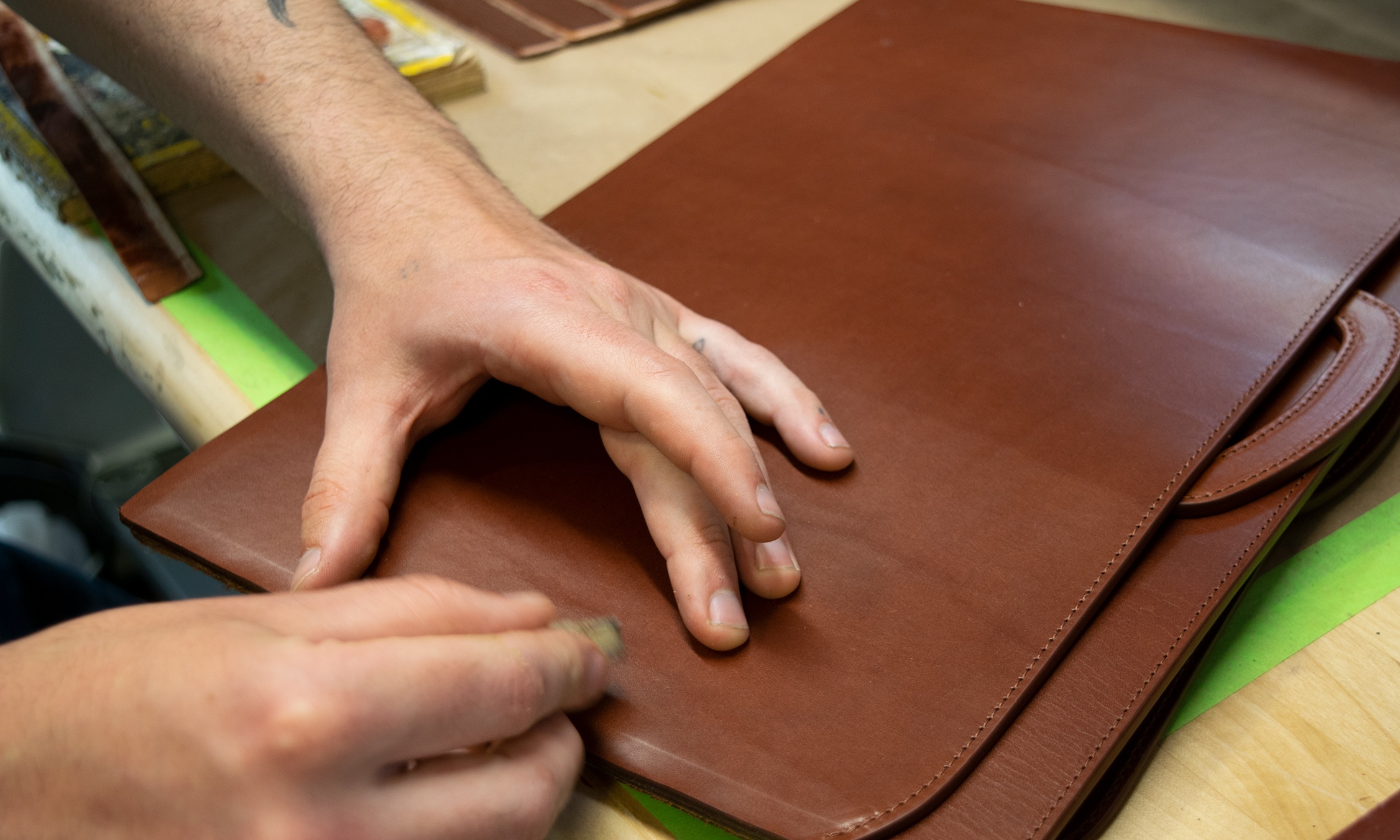
After that part is done, they apply a thin layer of glue to the edges of the sides before affixing them together for good, which is necessary so that the pieces can form a tight bond before being passed under the sewing machine. Because the Wells is made of bridle leather, this is especially important: bridle’s sleek nature makes it more prone to sliding out of line while being stitched, and so having the sides already secured and correctly positioned adds a layer of security to the process. These briefcases will soon begin to take shape—check back next week to see what stage they’ve reached!
Leave a Comment